WE’RE SENDING YOU TO AN EXTERNAL SITE TO APPLY
Please verify the following information to apply to this job
PROCESSING APPLICATION
Hold tight! We’re comparing your resume to the job requirements…
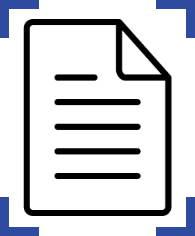
ARE YOU SURE YOU WANT TO APPLY TO THIS JOB?
Based on your Resume, it doesn't look like you meet the requirements from the employer. You can still apply if you think you’re a fit.
Job Requirements of Process Engineer:
- Bachelor’s degree in Mechanical, Electrical or Industrial Engineering
- Minimum of 3-5 years’ process engineering experience in a manufacturing environment, preferably within the tissue and/or paper industry
- Experience in Lean manufacturing techniques. Strong leadership skills with the ability to communicate lean manufacturing philosophy, vision and expectations. Ability to conduct and audit time studies to identify best practices and develop standard work procedures while driving safety, quality and productivity.
- Experience in troubleshooting mechanical drive systems, general machine design, engineering calculations, packaging equipment and manufacturing support equipment
- Strong computer literacy/competency including MS Office and statistical analysis tools.
- Excellent communication skills including both verbal and written.
- Ability to work independently and to execute programs in a cross functional environment
- Must have proven complex analytical skills as well as the ability to develop sound recommendations and solutions
- Organizational and prioritization skills
- Ability to read and understand machine drawings and/or schematic diagrams.
- Demonstrated ability to be proactive in problem solving and to lead the resolution of problems
- Ability to plan and organize work activities, manage work time efficiently and work independently
- Must be flexible and responsive to the needs of the department/facility/business
- Ability to partner with managers and employees to positively impact business results
- Core Competencies should include: Safe Work Habits, Quality Orientation, Creative and Innovative Thinking, Problem Solving, Research and Analysis, Operating Equipment, Ethics and Integrity, coaching and mentoring, Team Work, Time Management, Development and Continual Learning, Accountability and Dependability, Decision Making and Judgement, Providing consultation, Planning and Organizing, and Communication.
Kruger Products s an equal opportunity employer and encourages applications from all qualified individuals. Accommodation will be provided in all parts of the hiring process as required under Kruger Products' Accessibility Policy and Multi-Year Accessibility Plan - 1.04.33. Applicants need to make their needs known in advance.
We thank all applicants for their interest in Kruger Products but only candidates selected for an interview will be contacted.
Do you meet the requirements for this job?
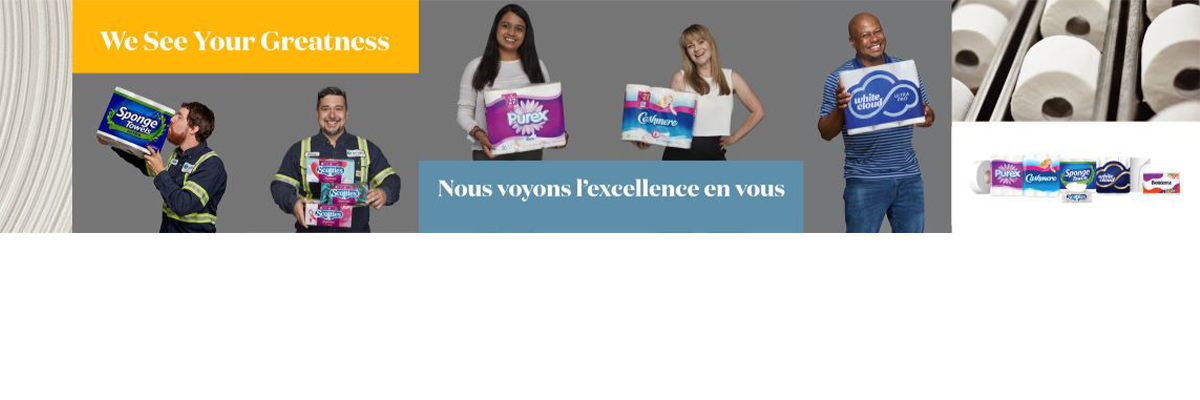
Process Engineer
The Process Engineer – works closely with department leaders to identify issues and opportunities and to respond quickly to operational problems. The incumbent will work closely with Maintenance and Operating Technicians for troubleshooting, maintenance and project work. The Process Engineer is an integral member of the Operation Excellence Team and will support the continuous improvement of the manufacturing processes of the Kruger AFH division.
- Establish and lead systems to support the transfer and integration of production data information, customization of Manufacturing Execution Systems (MES) and Enterprise Resource Planning (ERP) systems and assist with Human Machine Interface (HMI) customization for machine control
- Work collaboratively with:
- Converting Asset Leaders to develop automated production data entry and reporting systems to aid operations in improvement efforts
- Business Teams, Engineering and Maintenance for various system implementation, customization and support
- Identify and solve bottle-necks and variability within the process as related to manufacturing control systems and equipment capability through the introduction of industry proven tools (LEAN, 5S, Six Sigma etc.)
- Create and use processes for analysis of production and maintenance data to identify problems with processes, equipment, tooling, and personnel. Use technical skills and formal methods to identify root causes and implement solutions, including design changes.
- Develop technology approaches which support improved plant efficiency, process improvement and manufacturing flexibility
- Drive improvement of machine reliability and uptime.
- Optimize material specifications and conduct qualification trials
- Support the converting Asset Leaders in the development of machine centerlines
- Support equipment installation, modification and start-up activities, provide process engineering leadership to resolve problems, troubleshoot and optimize the installation process to meet project objectives and schedules
- Support the development and maintenance of process design standards and specifications for the manufacturing equipment and the plant utilities equipment and processes
- Support the development and implementation of training programs for operations, maintenance and engineering personnel to increase process knowledge, troubleshooting capability, and understanding of the overall manufacturing systems
- Develop knowledge and process expertise on Tissue converting equipment and plant utility and support equipment including tissue manufacturing, waste handling, compressed air and lubrication
- Supports the Reliability Engineer in performing failure analysis of equipment and devices and collaborates with the Maintenance Technicians to implement reliability improvement action items
- Develop specific technical procedures when necessary. Participate in Continuous Improvement efforts and teams.
- Conduct product, process and equipment qualification and capability studies
Job Requirements:
- Bachelor’s degree in Mechanical, Electrical or Industrial Engineering
- Minimum of 3-5 years’ process engineering experience in a manufacturing environment, preferably within the tissue and/or paper industry
- Experience in Lean manufacturing techniques. Strong leadership skills with the ability to communicate lean manufacturing philosophy, vision and expectations. Ability to conduct and audit time studies to identify best practices and develop standard work procedures while driving safety, quality and productivity.
- Experience in troubleshooting mechanical drive systems, general machine design, engineering calculations, packaging equipment and manufacturing support equipment
- Strong computer literacy/competency including MS Office and statistical analysis tools.
- Excellent communication skills including both verbal and written.
- Ability to work independently and to execute programs in a cross functional environment
- Must have proven complex analytical skills as well as the ability to develop sound recommendations and solutions
- Organizational and prioritization skills
- Ability to read and understand machine drawings and/or schematic diagrams.
- Demonstrated ability to be proactive in problem solving and to lead the resolution of problems
- Ability to plan and organize work activities, manage work time efficiently and work independently
- Must be flexible and responsive to the needs of the department/facility/business
- Ability to partner with managers and employees to positively impact business results
- Core Competencies should include: Safe Work Habits, Quality Orientation, Creative and Innovative Thinking, Problem Solving, Research and Analysis, Operating Equipment, Ethics and Integrity, coaching and mentoring, Team Work, Time Management, Development and Continual Learning, Accountability and Dependability, Decision Making and Judgement, Providing consultation, Planning and Organizing, and Communication.
Kruger Products s an equal opportunity employer and encourages applications from all qualified individuals. Accommodation will be provided in all parts of the hiring process as required under Kruger Products' Accessibility Policy and Multi-Year Accessibility Plan - 1.04.33. Applicants need to make their needs known in advance.
We thank all applicants for their interest in Kruger Products but only candidates selected for an interview will be contacted.